Vacuum Insulating Glazing (VIG) is an advanced insulating glass technology that offers outstanding thermal and acoustic performance, with significant advantages over traditional insulating glass. To achieve similar levels of insulation, VIG units are thinner, significantly lighter, and provide superior thermal and mechanical performance throughout their lifetime of over 25 years. Vacuum glass is also an excellent choice for sound insulation, as the vacuum layer between the glass panes effectively dampens the transmission of sound waves. In addition, vacuum glass can be combined with other glazing technologies to create hybrid structures.
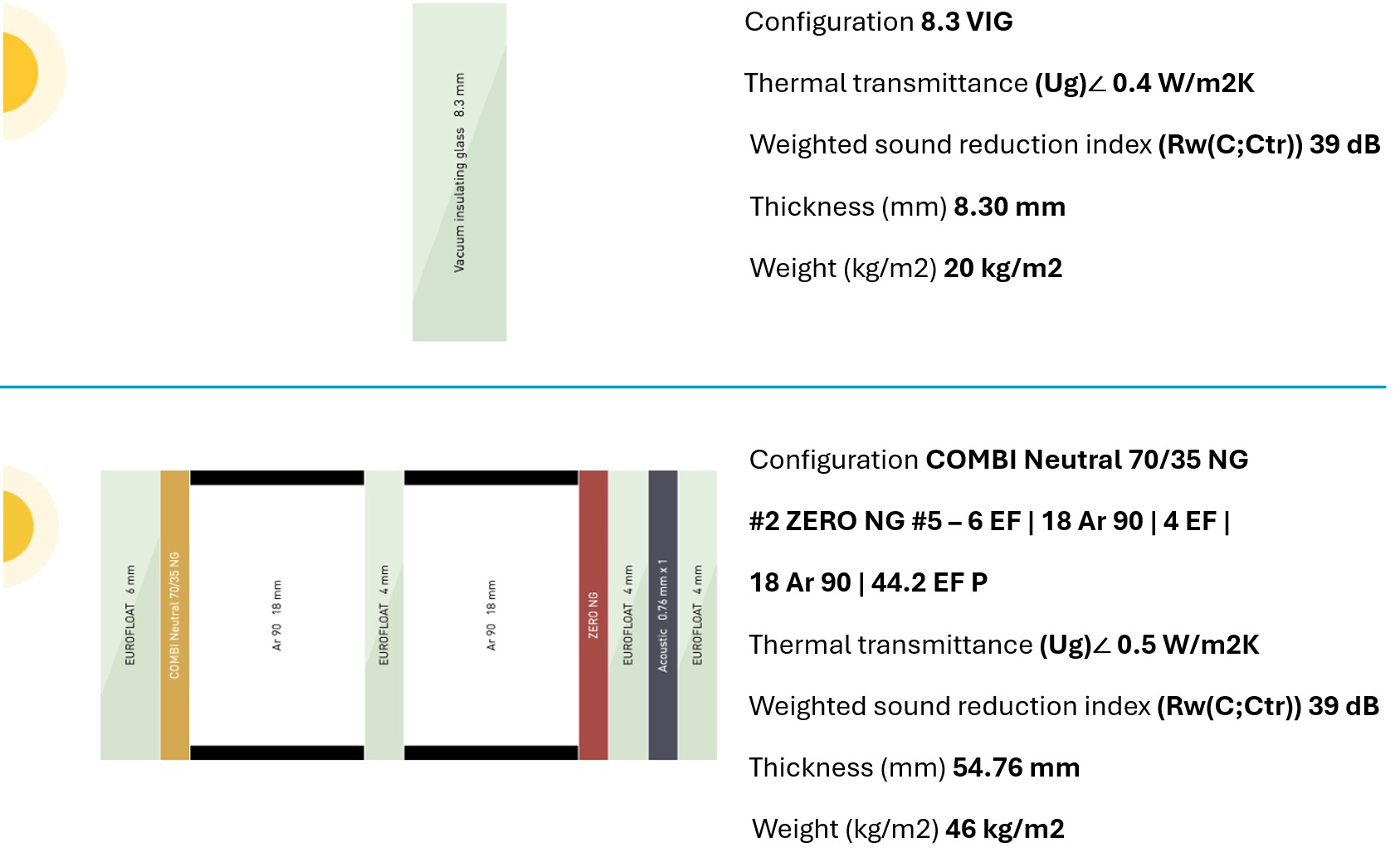
8.3 mm thick vacuum glass vs. 54.76 mm thick triple glazing with equivalent thermal and sound insulation performance.
Next-Generation Tempered Vacuum Glass
Vacuum glass itself is not a new invention – it has a long history in patent literature, with the first functional product introduced by the University of Sydney in the early 1990s. Over the years, vacuum glass manufacturing technology has improved in terms of both performance and aesthetics. A good example is the LandVac tempered vacuum glass, one of the most high-performing products on the market.
The latest generation of LandVac vacuum glass is manufactured using a patented lead-free metal edge seal, applied in a vacuum environment. There is no longer a need to drill holes for vacuum valves or getters. The surface is completely flat, making additional processing, such as lamination, easier. The visible area has been maximized, and the glass can be installed in a standard 12 mm glazing rebate. As a safety glass, tempered vacuum glass can withstand large temperature differences and bending stress without breaking. Available dimensions range from a minimum of 190 x 230 mm to a maximum of 1500 x 2500 mm, with total glass thicknesses of 8.3 mm, 10.3 mm, and 12.3 mm.
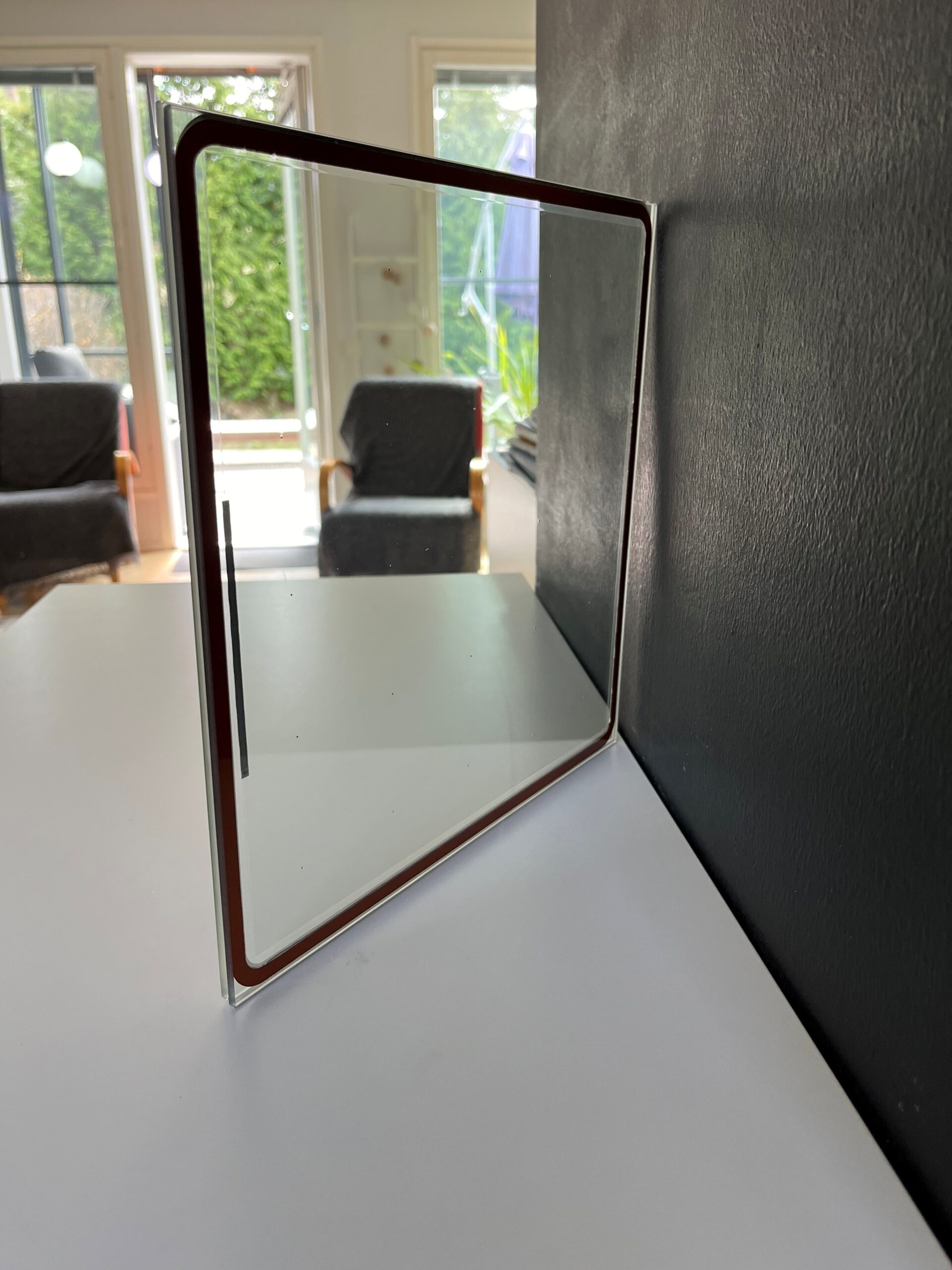
8.3 mm LandVac vacuum glass is completely flat and can be installed in a 12 mm glazing rebate.
Structure of Tempered Vacuum Glass
Vacuum glass consists of two sheets of tempered glass with a vacuum drawn between them, eliminating any gas that could transfer heat through conduction or convection. The vacuum also slows the propagation of sound and effectively reduces noise. In the LandVac unit, the distance between the glass panes is approximately 0.3 mm. Support pillars (∅ approx. 0.5 mm), spaced 55 mm apart, prevent the panes from touching. The glass edges are hermetically sealed with a flexible metal seal to maintain a stable vacuum level of 0.1 Pa and completely block gas infiltration.
The main parameters that define the unit’s low thermal transmittance (U-value of 0.4 W/m²K) are:
- Size and shape of the support pillars
- Pillar spacing
- Type of low-e coating
- Vacuum level (0.1 Pa)
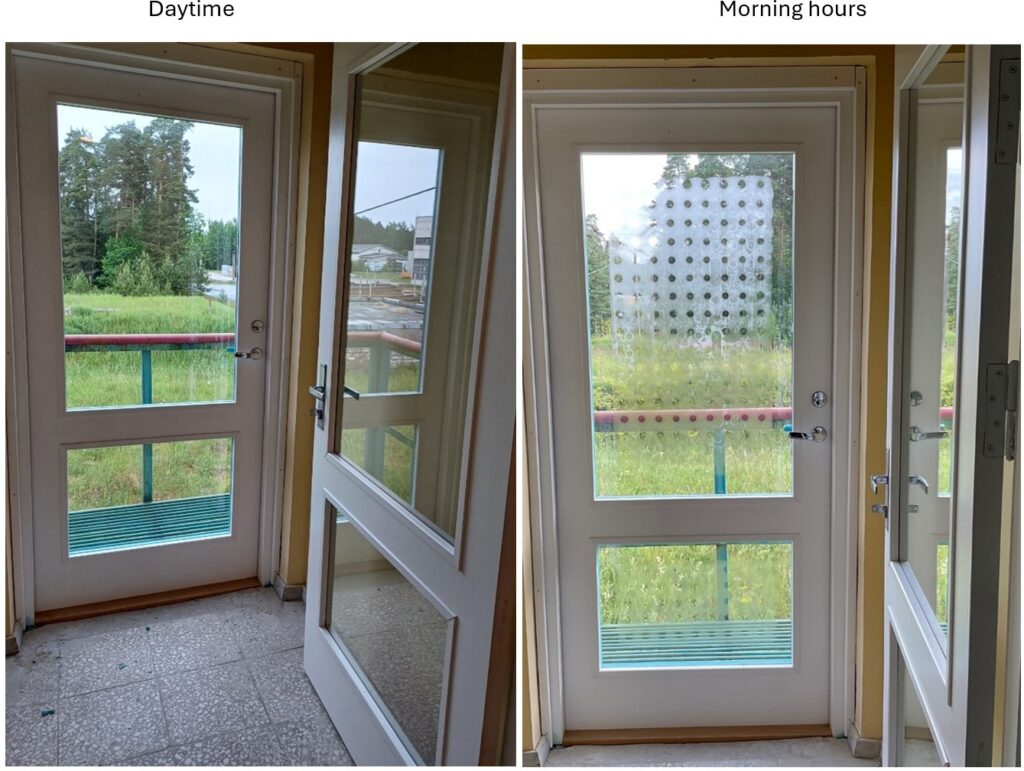
In tempered LandVac vacuum glass, a 55 mm pillar spacing can be used, resulting in one of the lowest U-values on the market.
Superior Acoustic Insulation
Vacuum glass offers exceptional acoustic insulation due to the vacuum layer’s ability to block sound waves. For example, an 8.3 mm thick LandVac unit achieves a weighted sound reduction index (Rw) of 39 dB. Additionally, its structure is highly effective against mid- and low-frequency noise such as traffic and construction noise. Acoustic performance can be further enhanced by laminating the glass with different thicknesses, using interlayers such as PVB, EVA, or SentryGlass, either via vacuum bagging or LamiPress techniques.
A Dream for Glass Processors – Limitless Applications
As a safety glass with superior thermal and acoustic insulation, tempered vacuum glass is ideal for green buildings, especially in urban environments. It can be used in doors, windows, conservatories, façades, and skylights in high-end residential and commercial buildings, public spaces, and landmark architecture. It’s also suitable for noise-insulating doors and windows, modern greenhouses, solar energy generation with transparent photovoltaic panels, and shipbuilding. Its lightweight and anti-fogging properties also make it an excellent choice for refrigerated display cases.
Looking Ahead
The durability and performance of vacuum glass under thermal and pressure loads have been extensively studied, and relevant ISO standards (ISO 19916-1:2018 and 19916-3:2021) are now in place [1].
Currently, the cost of vacuum glass remains high compared to traditional insulating glass. However, major glass manufacturers are investing in R&D to further develop this technology and reduce costs. The future lies in hybrid window concepts (IGU + VIG), improved cost-efficiency, and broader awareness and acceptance of vacuum technology across industries and consumers. With lower prices, vacuum glass could have a major impact on the retrofit market for existing buildings [2].
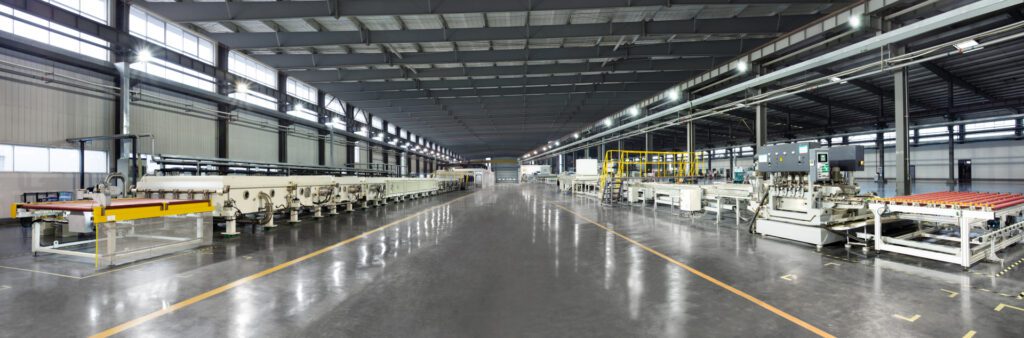
[1] Source: Challenging Glass Conference Proceedings – Volume 8 – 2022 – Belis, Bos & Louter (Eds.)
[2] Source: GPD 2019 Conference Proceedings, The Past, Present, and Future of the Vacuum Insulated Glazing Technology, Dr Cenk Kocer, University of Sydney, School of Physics, Sydney 2006, ss. 288-292.